こんにちは!IT解決コラム編集部です。
「人手不足で搬送作業が回らない」「重労働をロボットで効率化できないか」そんな課題を感じていませんか?
近年では、工場向け搬送・配膳ロボットの導入によって、作業負担を軽減し、業務の効率化を実現する企業が増えています。
人手不足や作業の非効率に課題を感じている現場にとって、ロボット導入はその解決策のひとつとなるかもしれません。
たとえば、次のような悩みを抱えていませんか?
- 搬送業務をもっと効率化したい
- 人手不足に悩んでいるが、コストはできるだけ抑えたい
- 搬送業務が自動化されておらず、常に人手が足りない
- 搬送ミスが多く、作業の負担が増えている
- ロボットを導入しても効果があるのか不安
搬送・配膳ロボットといえば、飲食店のイメージが強いかもしれませんが、実は工場でも生産効率を向上させるために導入されるケースが増えています。
本記事では、工場向け搬送・配膳ロボットの導入メリットや活用事例をわかりやすくご紹介します。
導入をご検討の方は、ぜひ参考にしてみてください。
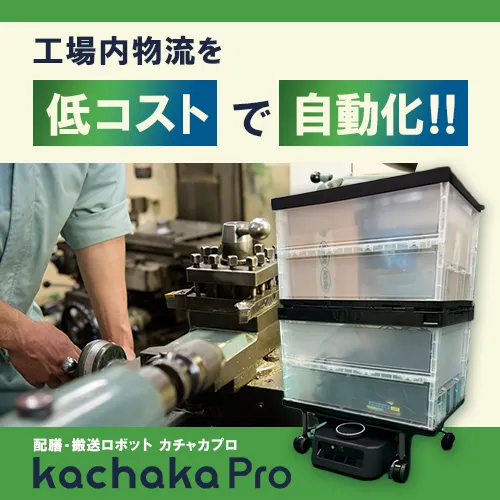
工場に搬送・配膳ロボットを導入するメリット
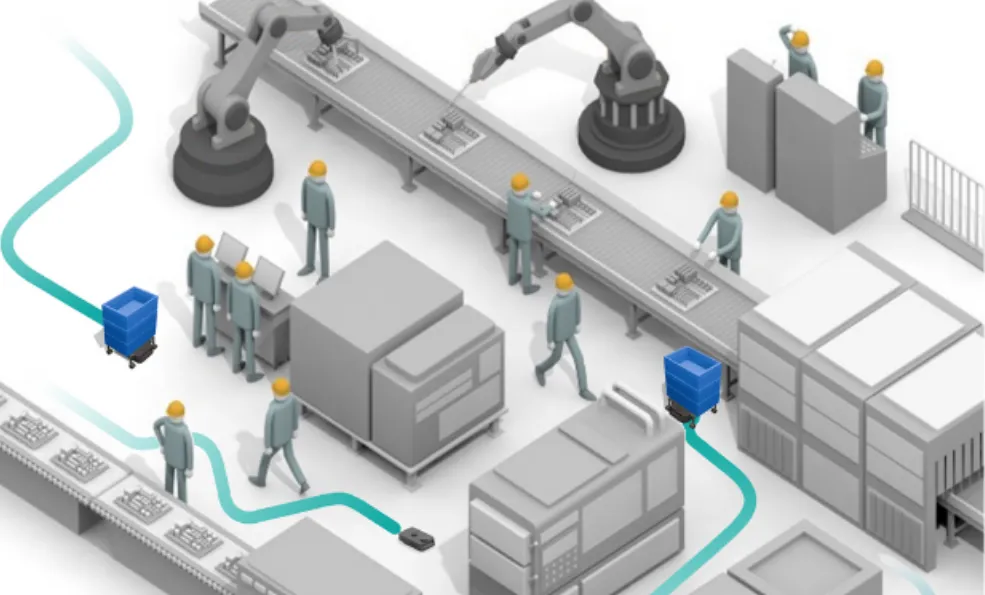
工場では、部品や材料を決められた場所へ運ぶ搬送作業が日常的に行われています。
しかし、深刻化する人手不足の影響で、搬送にかかる時間や労力が増え、作業効率の低下や人的コストの増加が大きな課題となっています。
こうした現場の課題を解決する手段として、搬送・配膳ロボットの導入が注目されています。
ここでは、工場にロボットを導入することによる、具体的なメリットをご紹介します。
効率と生産性の向上
搬送・配膳ロボットを導入することで、作業員が部品や材料を取りに行く手間が減り、作業の効率化が期待できます。
例えば、北海道ロジサービス株式会社では、搬送ロボットを導入したことで、作業員の移動距離が従来の6分の1に減り、作業時間を大幅に削減することに成功しています。
参考:ZMP「お客様の導入事例|北海道ロジサービス株式会社」
搬送・配膳ロボットは、移動時間の短縮に加え、シンプルな操作性と高い利便性を兼ね備えています。
中には、55㎝の通路幅でも通れる小型機種もあり、中小規模の工場でも導入しやすくなっています。
実際に工場内でロボットが稼働している様子を収めた動画がSNSで公開されていますので、ご紹介します。
サンテックスのデモ機に新しい搬送ロボットkachaka Pro
— 株式会社サンテックス【公式】 FA機器販売 自動化コンサルティング (@suntex_saitama) July 19, 2024
が加わりました✨
24㎝×39㎝の小型なボディながら
キャスター付きの専用棚の利用で30kgまで運ぶことができます🤖
55cmの通路でも通ることができるため
大型のAMRの導入が難しい事務所・工場でも活用できます☺#企業公式相互フォロー #製造業 pic.twitter.com/NY34nEKc80
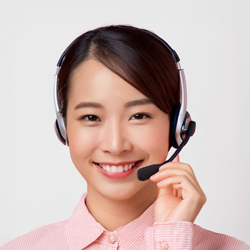
動画をご覧いただくとわかるように、スマートフォンで誰でも簡単に操作できるため、導入後の教育コストがほとんどかからないのも嬉しいメリットです!
ヒューマンエラー対策
工場における搬送作業では、部品の入れ間違いや搬送ミスが原因で、生産ラインの停止や品質トラブルにつながることがあります。
特に、人手不足による作業負担の増加が、ヒューマンエラーの発生を招く点が大きな課題です。
このような課題への対策として、搬送・配膳ロボットを導入することで、人手に頼っていた搬送作業を自動化でき、作業負担の軽減やミスの防止につなげることができます。
例えば、オムロン草津工場では、多品種少量生産の現場で、製品が1個だけ入った非効率な箱も人手で運ぶ必要があり、人材不足が大きな課題となっていました。
この課題に対応するため搬送・配膳ロボットを導入した結果、搬送作業の75%を自動化でき、リードタイムを平均80%短縮に成功。搬送業務の効率化と人手不足の解消に大きく貢献しています。
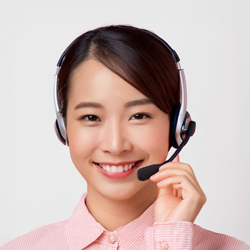
搬送・配膳ロボットといえば飲食店のイメージが強かったですが、こうした実績を見ると、工場でも十分に力を発揮していることがよくわかりますね!
他の業界での活用事例については、下記の記事もあわせてご覧ください。
関連記事:【解説】搬送・配膳ロボットの効果的な使い方とは?幅広い業種の活用事例
工場での搬送・配膳ロボットの活用事例
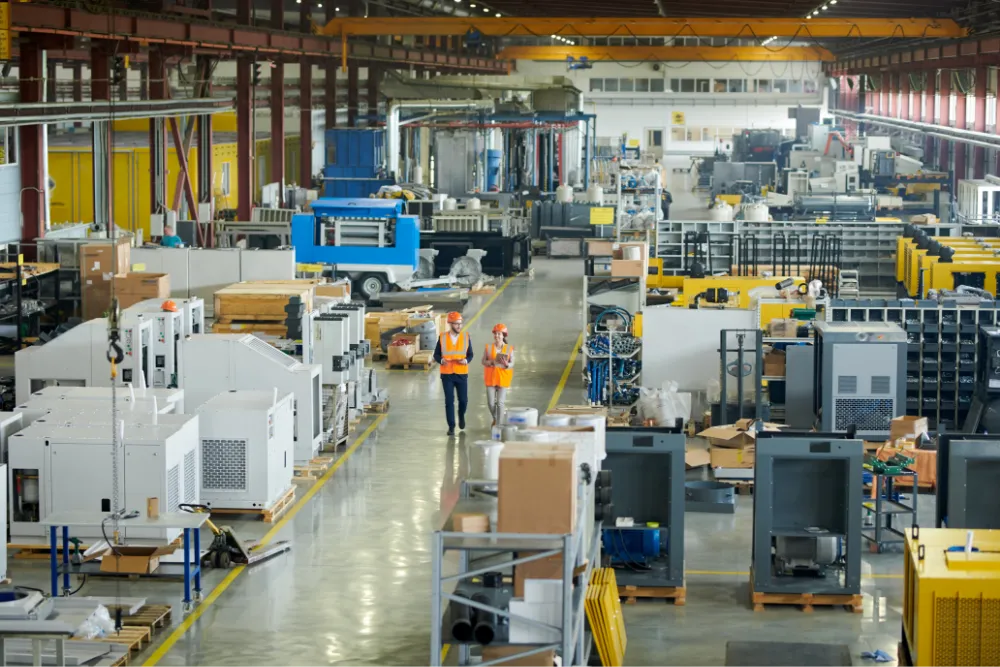
ここまで、搬送・配膳ロボットのメリットについて、事例も交えながらご紹介してきました。
ここからは、実際にロボットを導入した工場の具体的な事例をもとに、導入によってどのような成果が得られたのかをご紹介します。
活用事例①:大手電子部品メーカー
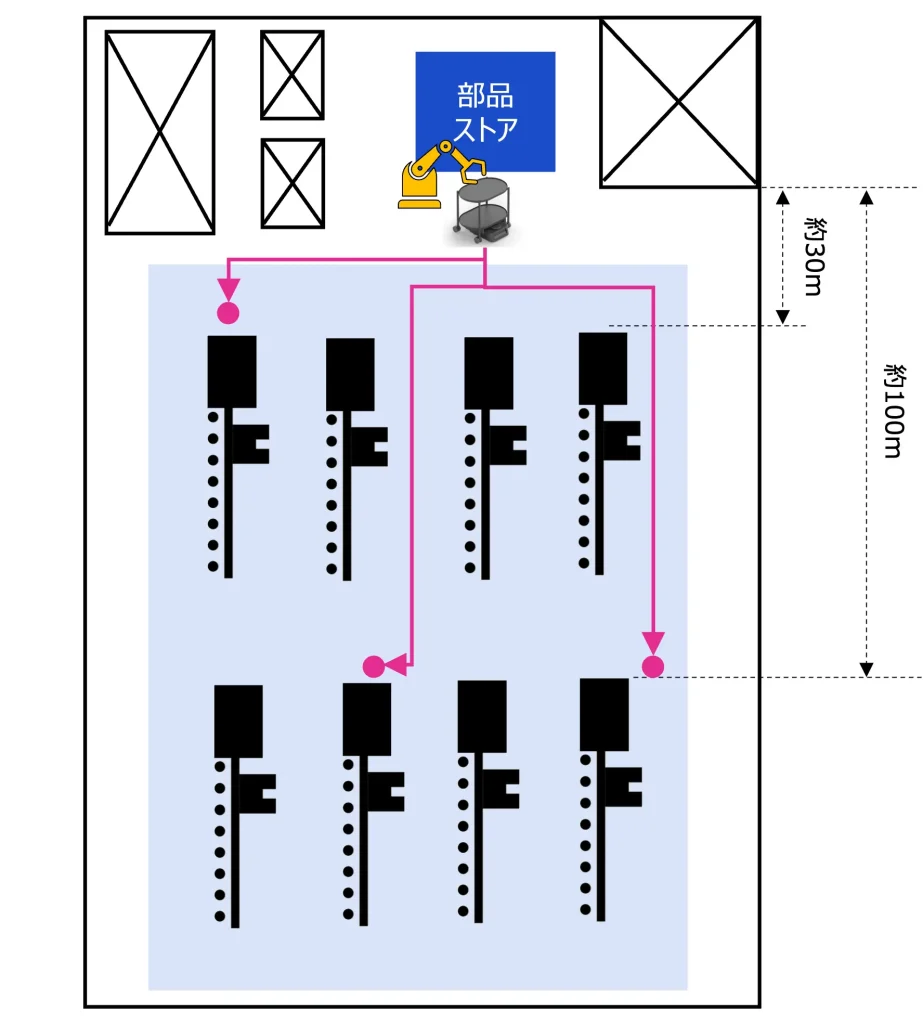
この電子部品メーカーでは、部品ストアから実装ラインへの部品搬送を作業者が手作業で行っており、毎回移動する手間が生産効率の低下につながっていました。
特に、最長100mの搬送距離を1日に何度も往復する必要があり、作業負担が大きな問題となっていました。
そこで、搬送・配膳ロボットを2台導入し、APIを活用した自動搬送システムを構築。
作業者がハンディ端末で部品の出庫を指示すると、部品ストアのマニピュレータがロボットに部品を積み込み、上位システムの指示通りに実装ラインまで正確に搬送する仕組みを導入しました。
導入による効果
- 搬送業務の自動化により、作業者の移動時間を月間44時間削減。人件費換算で約34.5万円/月のコスト削減を実現。
- API連携により、作業者の手を介さずに部品を搬送できるため、誤搬送や部品の取り違えが発生するリスクを低減。
部品の搬送にかかる負担を減らしながら、生産ラインの安定稼働と業務効率の向上を同時に実現しました。
活用事例②:大手自動車部品メーカー
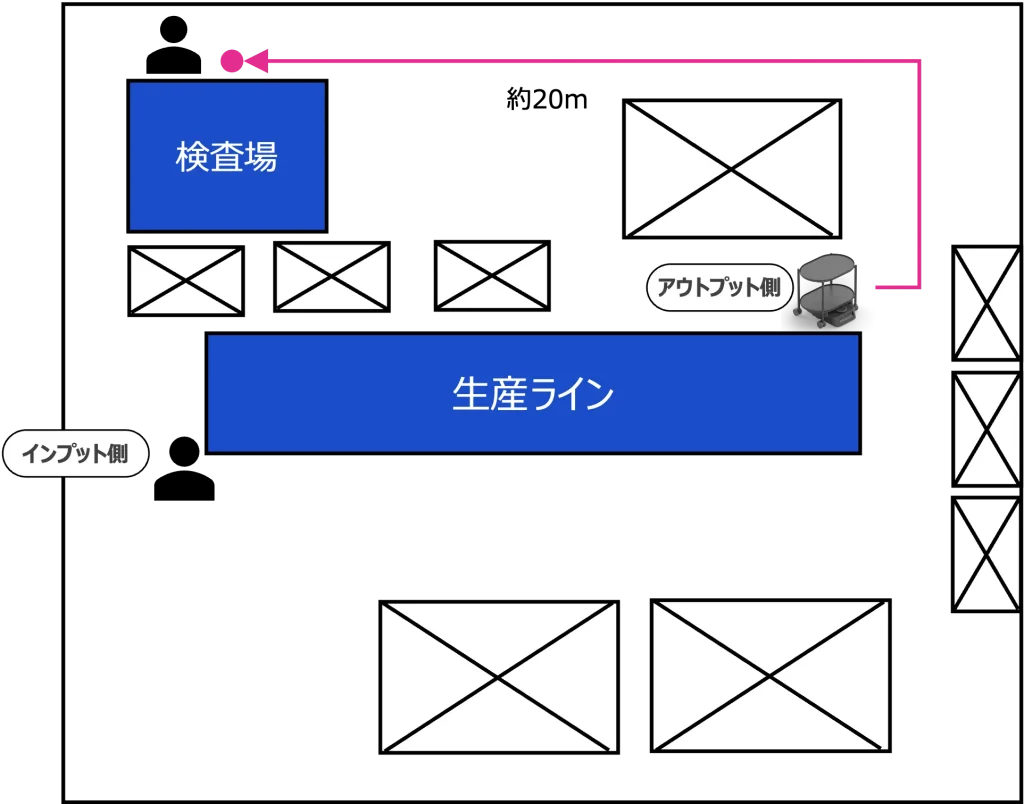
この工場では、完成品を検査場へ搬送する作業を作業者が手作業で行っており、片道20mの距離を1日に何度も往復しなければならない状況が、作業負担の増加につながっていました。
この課題を解決するため、搬送・配膳ロボットを1台導入し、自動搬送システムを構築。
完成品がコンベアから出てくると、ロボットが待機して受け取り、作業者がボタンを押すだけで検査場へ搬送される仕組みを導入しました。
導入による効果
- 作業者の移動時間が月間20時間削減され、人件費換算で約15.7万円/月のコスト削減を達成。
- ボタンを操作するだけで搬送できるため、作業の負担が軽減。
- 搬送の遅延がなくなり、生産ラインがより安定。
ロボットの導入により、搬送作業の負担がなくなり、作業者は生産ラインの業務に集中できる環境が整いました。
活用事例③:樹脂部品工場
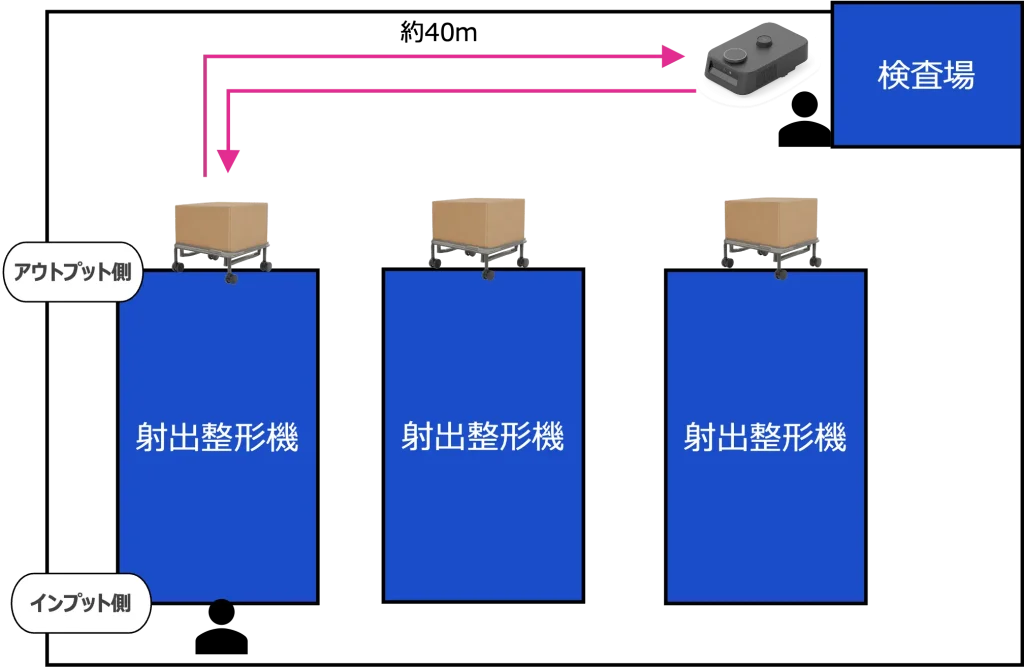
この工場では、樹脂成形部品を検査場へ搬送する作業を、作業者が手作業で行っており、移動時間のロスが課題となっていました。
そこで、搬送・配膳ロボットを1台導入し、部品搬送を自動化。検査場の作業者もボタンを押すだけでロボットが元の位置に戻る仕組みを採用しました。
導入による効果
- 作業者の移動時間を月間30時間削減。人件費換算で約23.5万円/月のコスト削減を実現。
- 軽量部品の頻繁な搬送が不要になり、作業者が本来の業務に集中しやすい環境を整備。
- ボタン操作だけで搬送が完了するため、導入直後からスムーズに運用可能。
導入前は、作業者が部品搬送に時間を取られ、本来の業務に十分な時間を確保できない状態が続いていました。
搬送・配膳ロボットの導入により、作業の負担と人件費の削減を同時に実現しました。
カチャカプロならコストを抑えつつ工場を効率化
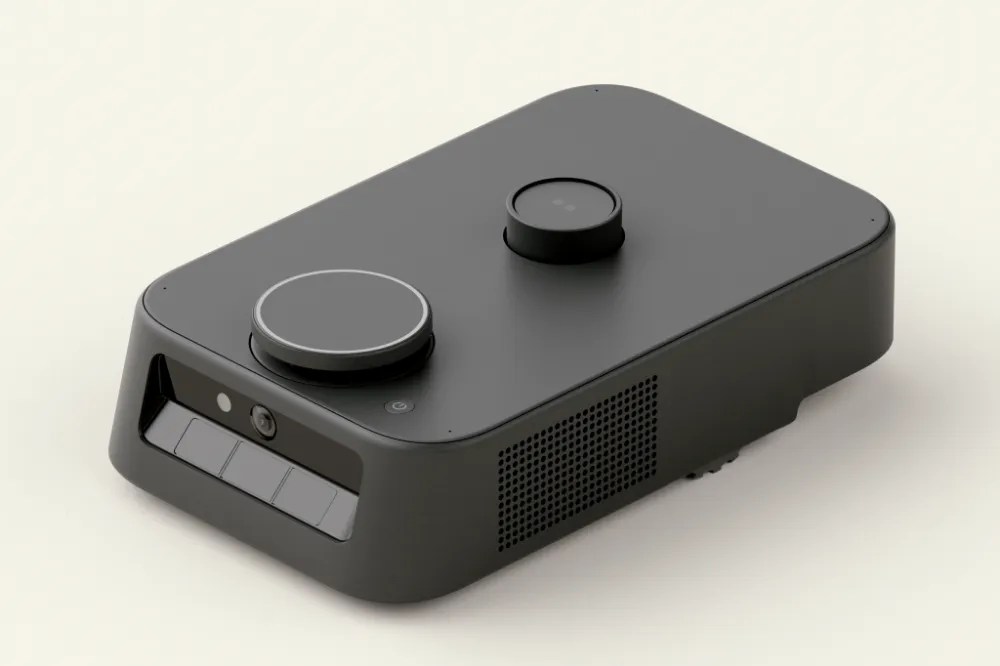
ここまで搬送・配膳ロボットのメリットや活用事例をご紹介してきました。
「これなら導入してみたいかも」と思った方もいらっしゃるかもしれませんが、実際に導入を検討するとなると、次のような不安を感じる方も少なくありません。
- 導入したいけれど、予算の確保が難しい
- 設定が複雑そうで、現場で本当に使いこなせるか不安
- 工場のレイアウトや環境に対応できるのか分からない
- 通路が狭く、ロボットがスムーズに走行できるか不安
なかでもコスト面は多くの企業にとって大きなハードルです。従来の搬送ロボットは高額なものが多く、投資回収に時間がかかるため、導入をためらうケースもあります。
しかし、「カチャカプロ」は業界最安水準※の価格で導入可能なうえ、狭い通路にも対応できるコンパクト設計と誰でも使えるシンプルな操作性を兼ね備えており、初めての導入にもぴったりです。
ここからは、低コストで工場の効率化を実現できる「カチャカプロ」の特徴をご紹介します。
※2024年2月メーカー調べ
導入しやすい価格設定(業界最安水準※)
カチャカプロは、100万円以下で導入可能な、業界最安水準の搬送・配膳ロボットです。
一般的な搬送・配膳ロボットは1台あたり数百万円以上するケースも多く、初期投資の負担が大きいため、導入をためらう工場も少なくありません。
その点、カチャカプロは家庭向けロボット「カチャカ」で培った技術を応用し、ハードウェアとソフトウェアの最適化によって大幅なコストダウンを実現。これにより、投資回収期間の短縮が可能となり、限られた予算でも導入しやすい価格を実現しています。
※2024年2月メーカー調べ
安価でも高性能
カチャカプロは、低価格でありながら機能面でも優れた搬送・配膳ロボットです。
以下のような特長があり、さまざまな工場環境での活用が期待できます。
- 複数の棚を効率的に運用可能
ドッキング機構により棚との分離・結合ができ、1台で複数の棚を柔軟に使い分けることが可能。 - APIによる柔軟なシステム連携
公開APIを活用することで、既存のシステムやIoTデバイスとのスムーズな連携が可能。 - 広い空間でも安定稼働
最大12mの測距が可能なLiDARを搭載し、大規模な工場や倉庫でも安定した走行・運用が可能。 - 高い安全性
障害物だけでなく、人の動きも検知して回避できる設計で、安全性にも配慮。
※LiDAR(ライダー)とは、「Light Detection and Ranging」の略で、レーザーを用いて周囲の環境を高精度に測定するセンサー技術です。レーザー光を照射し、対象物に反射して戻ってくる時間を計測することで、距離や形状を把握できます。
通常、このクラスの搬送・配膳ロボットは数百万円を超える価格帯が一般的ですが、カチャカプロであれば、低価格ながらもこうした高性能を兼ね備えています。
そのため、コスト面がネックで導入を見送っていた工場にも導入しやすい製品です。
搬送・配膳ロボットの導入による人件費との比較について詳しく知りたい方はこちらの記事をご覧ください。
関連記事:搬送・配膳ロボットの価格は?人件費との比較や導入時の注意点を解説
コンパクト設計で狭い通路にも対応
搬送・配膳ロボットを導入する際、多くの工場では「既存のレイアウトを大きく変えずに導入したい」というニーズがあります。
しかし、一般的なAMR(自律走行搬送ロボット)はサイズが大きく、狭い通路では運用が難しい場合もあります。
その点、カチャカプロは、幅550mmの通路でもスムーズに走行できるコンパクト設計。
これまでのロボットでは通行が難しかった狭い通路でも、工場のレイアウトを大きく変えることなく導入可能です。
簡単操作ですぐに使える
カチャカプロは、スマートフォンとWi-Fi環境があれば、特別な設備や専門知識なしですぐに運用開始できます。
専用アプリを使えば、マップの作成・棚の登録・目的地の設定といった初期設定が簡単に完了。
さらに、オプションの「カチャカボタン」を使えば、ボタンひとつで搬送指示を出せるため、作業員の負担も大幅に軽減されます。
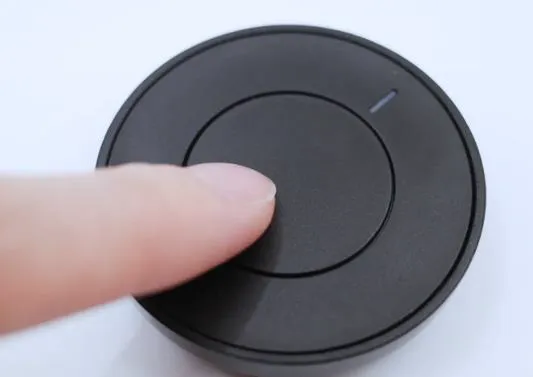
従来の搬送ロボットとの違いまとめ
製品名 | 導入・運用コスト | レイアウト変更 | 本体サイズ |
---|---|---|---|
カチャカプロ | 安価:100万円以下で購入可能 | 磁気テープやマーカ不要(AI + SLAM方式搭載) | 小型:最小550mmの狭路を走行可能 |
既存の搬送ロボット | 高額な導入費用・ランニングコストが必要 | レイアウト変更に磁気テープやマーカの設置が必要 | 本体が大きく、狭い通路では通行が難しい or 邪魔になることがある |
カチャカプロは「小型・安価・簡単」という特徴を備え、従来の搬送ロボットが抱えていた課題を解決する新しいAMR(自律走行搬送ロボット)です。
「自社でも使えるかわからない…」「導入後の運用方法が気になる…」といったご不安がある方は、ぜひお気軽にご相談ください。
当社担当者がおすすめの導入プランをご提案し、運用方法やコストについて詳しくご説明いたします!
まとめ
いかがでしたか?
本記事では、工場における搬送・配膳ロボットの導入のメリットについてご紹介しました。改めて本記事の内容をまとめると以下の通りです。
この記事の要点
● 搬送・配膳ロボットを導入することで、作業員の移動時間を削減し、生産性の向上が期待できる
● カチャカプロは小型・低コスト・簡単操作で、狭い工場内でも導入しやすい設計
● 搬送業務の自動化によって、ヒューマンエラーの削減や生産ラインの安定稼働にも貢献
当社が取り扱う搬送・配膳ロボットカチャカプロは、業務用途に必要な機能を十分に備えながら、業界最安水準の価格を実現しています。
さらに、工場や物流現場で活躍するロボット・AGVや、ロボット向けの部品・材料などが出展するロボット総合展「ロボデックス2024」にも出展され、工場や物流現場での活用が注目されています。
明日から幕張メッセで開催のロボデックス2024にて、PFR過去最大規模の展示を行います!
— Y.Nakayama/ Preferred Robotics電気エンジニア (@YotetsuNakayama) September 3, 2024
工場でもカチャカ!
PLCの出力ポートからタスクをトリガするデモも展示しております! https://t.co/Q9Og7jdQUT pic.twitter.com/etwFiNJYlH
工場に配膳・搬送ロボットを導入することで長期的なコスト削減効果も期待できます。導入のメリットを踏まえ、自社にとっての投資価値をぜひご検討ください。
お見積り依頼や無料相談を24時間365日受付中!
当社では、工場の規模や運用ニーズに合わせた搬送・配膳ロボットの導入をサポートしております。
「導入コストが気になる」「自社の環境で使えるか不安」という方も、ぜひお気軽にご相談ください。お見積りも無料で承っております。